
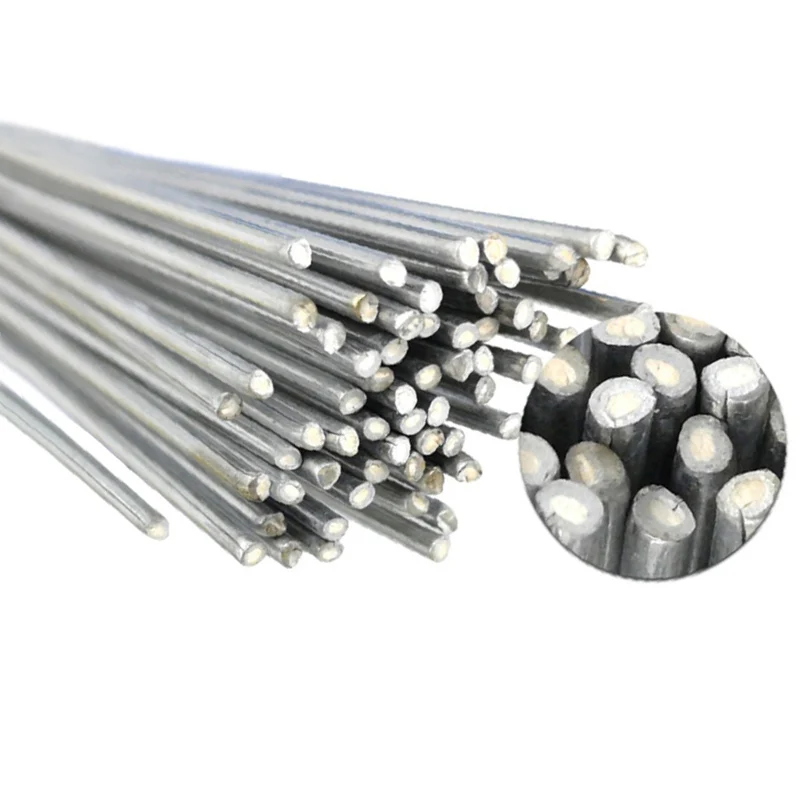
Please click here to view License Agreement for Educational Institutions. If you do not agree to the terms of this License Agreement, promptly exit this page This License Agreement, that you understand it and that you agree to be bound by its IMPORTANT-READ THESE TERMS CAREFULLY BEFORE DOWNLOADING THIS DOCUMENT.īy downloading the ASTM Document you are entering into a contract, and acknowledge that

Sound soldered joints that are adequately protected can be expected to give many years of satisfactory service in most environments. The resistance to corrosion of soldered joints in aluminum varies greatly, depending upon solder composition, joint design, use of protective coatings, and the environment in which the soldered joints are exposed. Of the performance characteristics, resistance to corrosion is by far the most important, although in some cases other factors may be of consequence. The use of soldering as a method for joining aluminum depends largely upon the performance required of the resultant joints. For some application, it may be desirable to plate the aluminum with copper, nickel or some other metal and then solder using procedures applicable to the plating metal. These include rub soldering, ultrasonic soldering, and reaction-flux soldering. Chloride-free organic fluxes can be used when soldering with low-temperature solders, but chloride-containing salt fluxes must be used when soldering with higher temperature solders.Īll of the common soldering techniques can be used in soldering aluminum and in addition, there are several techniques more applicable to aluminum than to other metals. Before soldering aluminum, the oxide film on the surface must be removed, either mechanically while the surface is covered with molten solder, or with fluxes. The solders for aluminum are usually alloys of zinc, tin, cadmium and lead, although small amounts of other elements have been added to many such solders. Aluminum can be soldered using a wide variety of solders, fluxes and techniques.
